FALLSTUDIE SAFRAN LANDING SYSTEMS
Safran Landing Systems (vorher bekannt als Messier-Bugatti-Dowty) ist Weltmarktführer in Design, Entwicklung, Produktion und Support für Luftfahrt-Fahrwerk-Systeme.
Eine einzigartige Kombination aus fortschrittlichen Engineering Fähigkeiten, integrierten System Technologien und Erfahrung in einer großen Auswahl an Programmen erlaubt es Safran Landing Systems innovative Lösungen für eine große Auswahl an Flugzeugen anzubieten.
NIKKEN wurde von dem Unternehmen im Jahr 2007 kontaktiert um gemeinsam an einem Projekt zur Optimierung der Produktion eines Schwinghebels für den Airbus A350 zu Arbeiten. Die finale Lösung erforderte die gleichzeitige Bearbeitung von 6 583 kg schweren Titan Schmiedeteilen auf einer vertikalen 6-Spindel Droop & Rein Maschine.
Die vorangegangene Applikation produzierte 3 Schwinghebel auf einer Maschine die von Hand indexiert werden musste. Jede Indexierung auf manueller Basis dauerte 15 Minuten und musste von einem Bediener innerhalb des Bearbeitungbereiches der Maschine ausgeführt werden – Definitiv keine Angenehme Lösung in einem Bereich der mit Titan Spänen und Kühlmittel behaftet war.
Die Integration von sechs Komponenten auf dem von sechs CNC-Rundtischen gestützten Maschinenbett erforderte einen ingenieurtechnischen Geniestreich. Da zwischen den Mitten der Komponenten 3500 mm Abstand lagen, mussten auf der Mitte des Maschinenbetts Nikken TAT320 Auflagetische Rücken an Rücken montiert werden. Damit wurde die Platzausnutzung optimiert, so dass der Abstand zwischen den Komponenten auf ein absolutes Minimum reduziert werden konnte. An jedem Ende des Betts wurden sechs Nikken CNC601B-Rundtische montiert, um für die Bearbeitung so viel Platz wie möglich zu schaffen. Falls bei einer Änderung der Anforderungen von Luftfahrzeugen größere Teile erforderlich werden und die Spezifikationsgrößen sich in Zukunft ändern sollten, ist mit diesem Layout ist auf dem Maschinenbett auch noch mehr Platz verfügbar.
Mit dem durch diesem Layout gewonnen Platz auf dem Maschinenbett ist es in Zukunft auch möglich auf dieser Maschine noch größere Bauteile zu fertigen sollten sich die Bedürfnisse ändern.
Durch die Integration der Rundachsen dauert jede Indexierung nur noch 15 Sekunden und es ist nicht mehr nötig das Maschinenbett zu betreten. Diese finale Lösung hat die Maschinenlaufzeit signifikant erhöht und in Verbindung mit 10 Werkzeugwechseln eine Zeitersparnis von mehreren Stunden erbracht. Mit Blick auf den Wert der 6 Komponenten ist es für Safran essentiell das der Prozess komplett Optimiert ist um 100% Genauigkeit zu liefern und gleichzeitig die Zyklus Zeiten zu minimieren.
Die CNC integrierung erfolgte durch Siemens mithilfe einer Siemens 840D Steuerung zum Betrieb der 6 Spindeln zusammen mit den & Rundachsen und Gegenlagern.
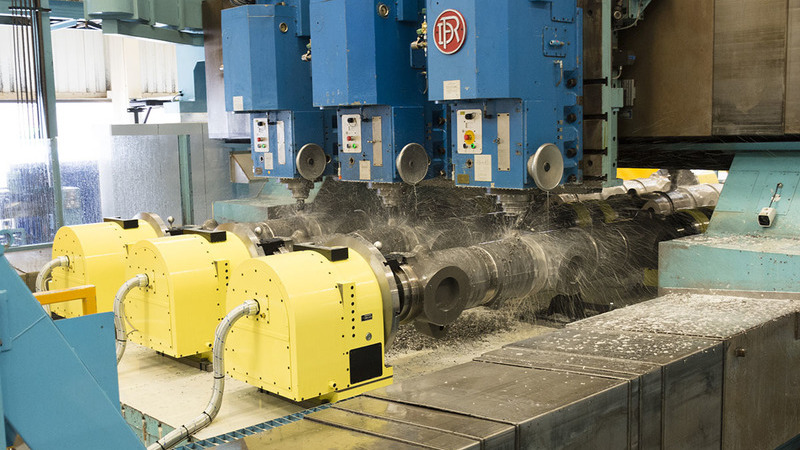
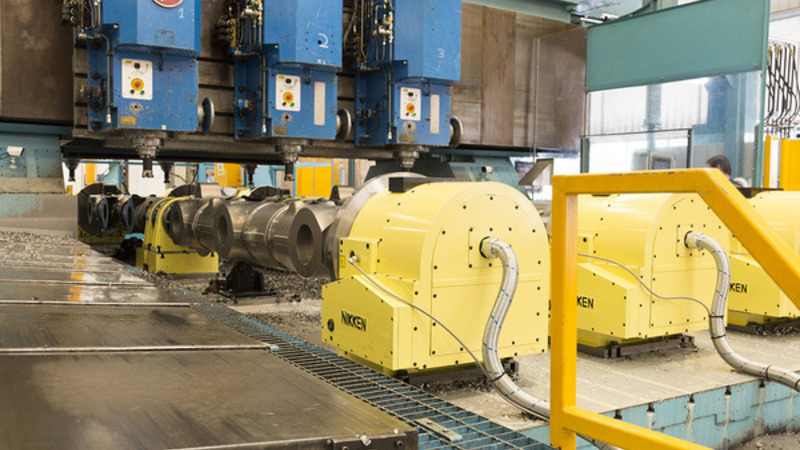
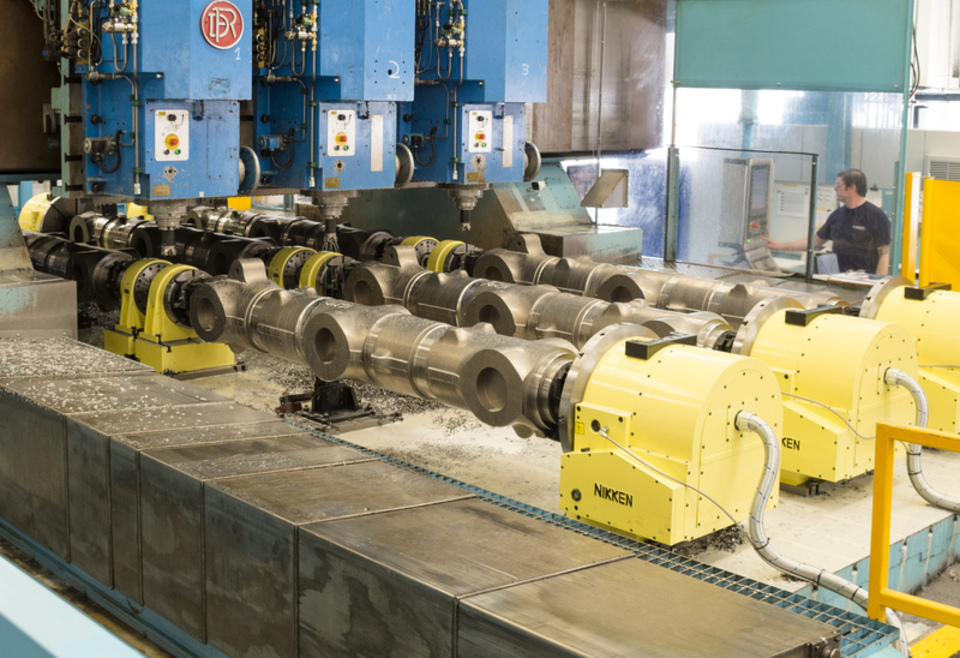