Tesla Engineering Ltd
Tesla Engineering entwirft und fertigt Magnete für Teilchenbeschleuniger, spezielle Gradientenspulen für MRT-Systeme und fortschrittliche supraleitende Magnete für neue Märkte wie Kernfusion, erneuerbare Energiequellen, Halbleiterverarbeitung und Krebstherapie.
Tesla wurde 1973 gegründet und hat seitdem Niederlassungen in den USA und den Niederlanden eröffnet. Allein im Vereinigten Königreich beschäftigt das Unternehmen über 300 Mitarbeiter. Nach einem rasanten Wachstum von über 25 % in den letzten Jahren ist die Arbeitsbelastung bei Tesla drastisch gestiegen, doch aufgrund der begrenzten Fläche musste eine Lösung gefunden werden, um die Effizienz der vorhandenen Maschinen zu steigern.
John O'Shea, Leiter der Maschinenwerkstatt, leitete das Projekt zur Rationalisierung der Maschinenwerkstatt und führte bei Tesla eine Schnellwechselvorrichtung für Werkstücke ein. Nachdem er verschiedene Lösungen für die Werkstückaufnahme untersucht hatte, wandte er sich an NIKKEN Business Manager Danny Wells, um eine Lösung zu finden.
Danny und das technische Team des NIKKEN Innovationszentrums arbeiteten mit Tesla zusammen, um eine Lösung zu entwickeln, die die Maschinenkapazitäten maximiert und gleichzeitig die Rüst- und Ladezeiten sowie die Eingriffe des Bedieners minimiert und den Metallausschuss reduziert.
Die vorgeschlagene Lösung besteht aus TRIAG-Schienen, die mit PowerClamp-Schraubstockmodulen ausgestattet sind und aus selbst entworfenen und hergestellten Paletten, auf denen das Schienensystem sitzt.
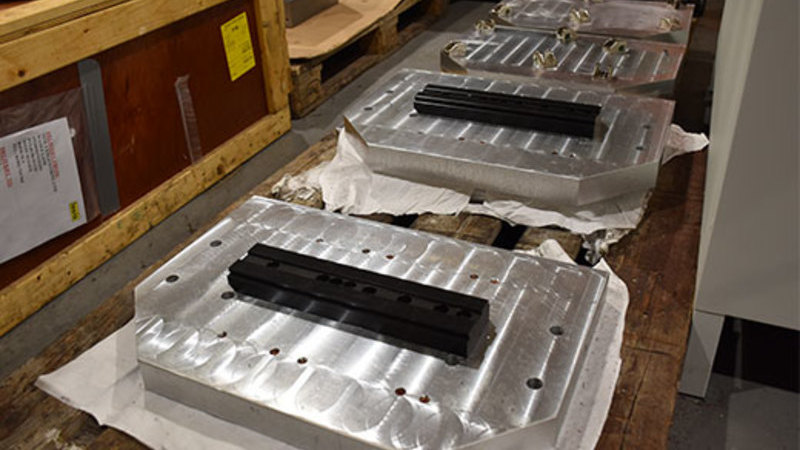
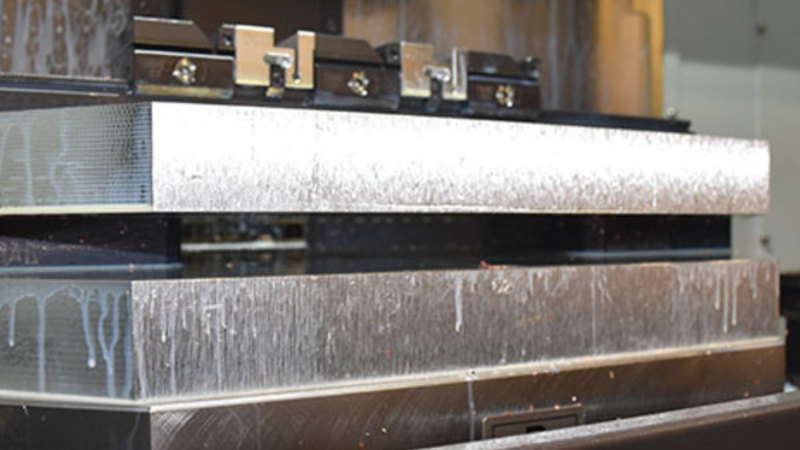
Die Lösung ermöglicht es Tesla, Paletten ohne Rüstzeiten auf die Maschine zu heben und von ihr zu nehmen, wobei der einzige Eingriff des Bedieners darin besteht, die Klammern je nach Auftrag zu wechseln. Tesla betreibt derzeit 2 Paletten auf einer Maschine, d. h. während der Bediener eine Palette belädt, schneidet die Maschine die andere Palette.
Die Minimierung der Bedienereingriffe hat sich enorm auf die Produktivität bei Tesla ausgewirkt. Das Einrichten eines Auftrags, das früher 4 bis 6 Stunden dauerte, kann dank der Schnellwechsellösung jetzt in nur 15 Minuten erledigt werden, ohne dass das Werkstück getaktet oder ein Bezugspunkt gesetzt werden muss, da der Bezugspunkt bereits vorhanden ist.
Die angebotene Lösung ist modular, d. h. sie kann auf die jeweilige Aufgabe zugeschnitten werden und bietet ein hohes Spannmoment. Tesla bearbeitet eine Vielzahl von Materialien, darunter auch Kupfer, so dass das hohe Spannmoment ein großer Vorteil war, da die Greiferbacken nur 3 mm des Materials halten mussten, während sie vorher mindestens 10 m halten mussten. Dies führte wiederum zu hohen Kosteneinsparungen.
Unsere durchschnittliche Rüstzeit betrug 4 Stunden und 25 % der Zykluszeit für das Beladen. Dank der Werkstückträgerlösung sind wir jetzt 50 % effizienter - John O'Shea
Seitdem Tesla die neue Lösung einsetzt, ist das Unternehmen so effizient geworden, dass ihm aufgrund der Produktionsgeschwindigkeit das Material ausgegangen ist. Nachdem Tesla bewiesen hat, dass diese Lösung auf einer kleineren Maschine funktioniert, wird das Unternehmen die Lösung auf eine Vielzahl von Maschinen ausweiten, was die Verschwendung von Materialien, die bis zu 150.000 Euro kosten, erheblich reduzieren wird.
Wenn Sie weitere Informationen zur Optimierung Ihrer Produktionslinie wünschen, zögern Sie nicht unser Expertenteam für ein Beratungsgespräch zu kontaktieren.