X-Cel Superturn Ltd
X-Cel Superturn Ltd. bietet einem weltweiten Kundenstamm qualitativ hochwertige Lösungen an und ist auf präzisionsbearbeitete Komponenten für die Petrochemie (einschließlich Bohrungen, Oberflächen- und Unterwasseranwendungen), die Energieerzeugung, die Luft- und Raumfahrt und die Bauindustrie spezialisiert.
X-Cel wandte sich an NIKKEN wegen einer bevorstehenden Anwendung, bei der einunddreißig Löcher mit einem Durchmesser von 3 mm und einer Tiefe von 44 mm im Inneren eines Bauteils bearbeitet werden sollten.
Dabei stellte sich heraus, dass eine 90°-Winkelkopflösung erforderlich war, um den erforderlichen Anfahrwinkel für diese Merkmale mit dem horizontalen Doosan NHM-Bearbeitungszentrum in Kombination mit den für den Rest des Teils erforderlichen zusätzlichen Fräsvorgängen zu erreichen.
Derzeit würde diese Art von Arbeit zwei Aufspannungen auf zwei verschiedenen Maschinen erfordern (die horizontale Maschine für den ersten Arbeitsgang und ein zweiter Arbeitsgang, der auf einem vertikalen Bearbeitungszentrum ausgeführt wird). Die NIKKEN/ALBERTI-Lösung hatte das Potenzial, eine einzige Aufspannung auf der horizontalen Maschine zu ermöglichen, wobei der Winkelkopf einen ähnlichen Bearbeitungsansatz wie auf der vertikalen Maschine bietet.
NIKKEN empfahl seine ultimative Spindeloptimierungslösung, die BT50-TH90cn-3.5 mit NIKKEN SK Spindelausgang. Damit kann der Kunde die Vorteile der präzisen Slim Chuck Spannzangen- und Mutterlösungen von NIKKEN nutzen. Diese Kombination verbessert nicht nur die Genauigkeit und Leistung drastisch, sondern der Winkelkopf ist auch in der Lage, einen maximalen Druck von 100 bar durch die Spindelkühlung zu liefern.
Der Hauptvorteil für den Kunden besteht darin, dass das Kühlmittel in Verbindung mit dem 'J-Type'-Muttersystem und der entsprechenden 'Jetter'-Kappe entweder durch das Schneidwerkzeug oder um das Schneidwerkzeug herum gesteuert werden kann.
NIKKEN lieferte die Werkzeuglösung auch als automatischen Werkzeugwechselkopf, der es dem Bediener ermöglicht, den Kopf bei Bedarf automatisch zu wechseln, was weitere Rüstzeit auf der Maschine spart.
In Verbindung mit dem Palettenwechsel auf der Maschine und der verbesserten Schneidumgebung, die durch den Alberti-Kopf erreicht wurde, konnten die Zykluszeiten eindrucksvoll von knapp über 1 Stunde auf 8 Minuten gesenkt werden, aber auch weitere Einsparungen durch die Bereitstellung zusätzlicher Bearbeitungskapazität auf einer VMC!
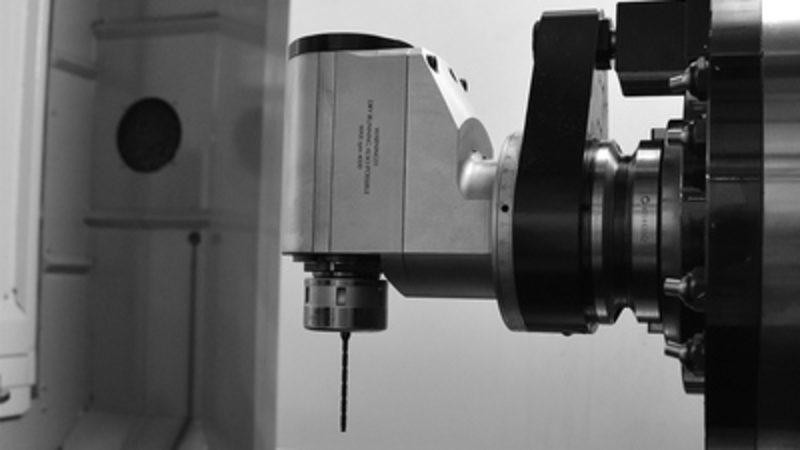
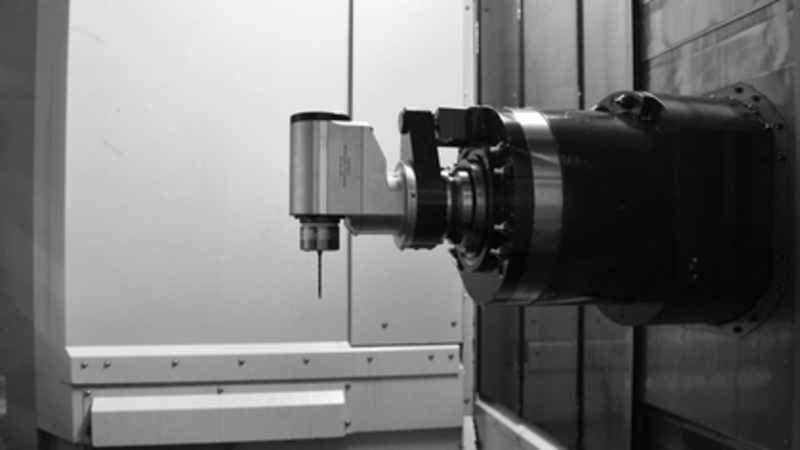