TWM TECHNOLOGY, DEVON - GROSSBRITANNIEN
Produktivitätssteigerung – Durch die Zusammenarbeit wurde eine Steigerung um fast 800 % erzielt
TWM Technology ist führend bei Design und Herstellung hermetischer High-End-Metallgehäusen und Bauteilen. Ihre 30-jährige Erfahrung und Kontinuität im Management stellen sicher, dass fundiertes Wissen und Erfahrung im Mittelpunkt ihrer Aktivitäten stehen. Sie bieten Kunden Gesamtlösungen, vom Design für die Herstellung bis zur Lieferung von Präzisionsprodukten innerhalb strikter Fristen.
Jez Pring, technischer Leiter von TWM, wandte sich an NIKKEN Kosakusho Europe Ltd., um einen Weg zur Verbesserung der Produktionsprozesse zu untersuchen, um den steigenden Mengenbedarf eines ihrer Kunden gerecht zu werden. Das betreffende Verfahren umfasste die Beladung und Bearbeitung eines komplexen Bauteils mit zwölf Werkzeugwechseln, ein Teil nach dem anderen. Für diesen Vorgang musste ein Bediener zum Laden und Entladen jedes Teils anwesend sein, was wertvolle Werkzeugmaschinenkapazität kostete.
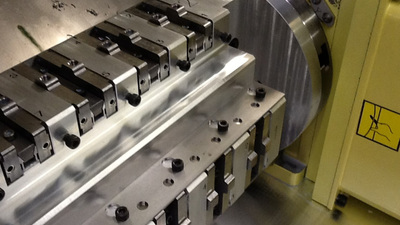.jpg)
CNC202 DREHTISCH MIT TAT170N UND EINGERICHTETER SCHWENKZAPFEN-FIXIERVORRICHTUNG.
Der Ansatz bestand darin, zu analysieren, wo Einsparungen erzielt werden können, und eine Lösung zu entwickeln, um die Effizienz ohne Kompromisse bei der Komponentenqualität zu maximieren. Andrew besuchte TMW und arbeitete mit ihnen zusammen, um die optimale Lösung zu entwickeln. Hierbei handelt es sich um einen CNC202-Drehtisch mit TAT170N und Spannbrücke. Dies war eine echte Teamleistung, bei der Andrew das Grundprinzip lieferte und Jez die Werkstück-Aufspannung entwickelte. Zusammengenommen ermöglichte dies das mehrfache Laden der Teile, wodurch die Anzahl der Vorgänge verringert wurde und die erforderlichen Prozessfortschritte erreicht und sogar übertroffen wurden.
Vor Umsetzung der Mehrfachaufspannung benötigte jedes Bauteil im Schnitt 16 Minuten zur Fertigung, und jeden Tag wurden durchschnittlich 28 davon fertiggestellt. Nach Umsetzung des Merfachaufspannung mit CNC202-Rundtisch und Spannbrücke sank die durchschnittliche Bearbeitungszeit pro Teil auf 2,5 Minuten, und die Tagesproduktion lag nun im Schnitt bei 216 Teilen. Durch die neue Bearbeitungslösung konnte nicht nur die Produktivität gesteigert werden, sondern es wurde auch 14 Stunden an Kapazitätsbindung eines qualifizierten Maschinenbedieners eingespart werden, der nun in dieser Zeit für andere Aufgaben eingesetzt werden konnte.
Im Rückblick auf das Projekt bemerkt Jez dazu: „Die Zusammenarbeit mit Andrew Bould und NIKKEN hat zu einer für unsere Zwecke optimalen Lösung geführt und sich bei dieser Anwendung enorm auf die Produktivität ausgewirkt. Das Vertrauen in NIKKENs bewährte Expertise und unerreichte Produktqualität hat zusammen mit TWMs Anwendungskenntnissen zu einer unschlagbaren Partnerschaft geführt, die auch bei zukünftigen Projekten noch wertvoll sein wird.“
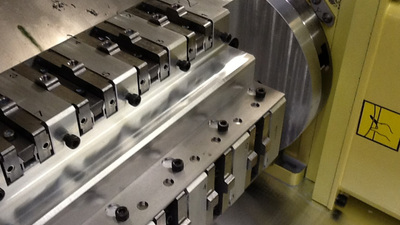.jpg)
CNC202-RUNDTISCH MIT TAT170N UND DREHZAPFENHALTERUNG.